Secondary Coupling Device: 10 Expert-Recommended Options for Durability
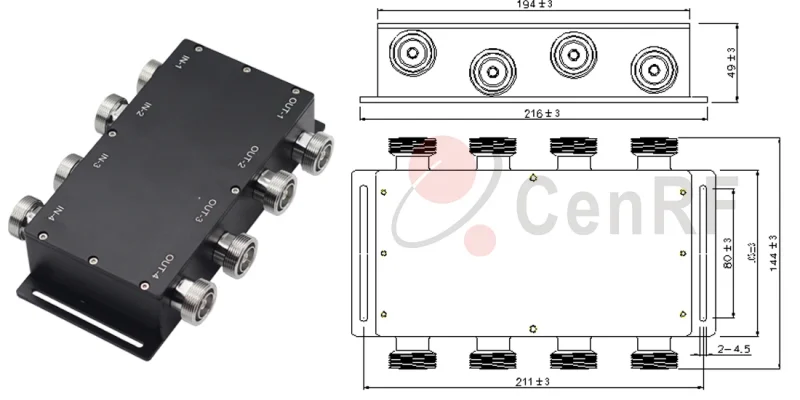
In the world of mechanical engineering and heavy-duty applications, secondary coupling devices play a crucial role in ensuring system reliability and performance. These devices are designed to provide additional support and stability, protecting primary components from excessive stress and potential failure. As industries increasingly demand higher efficiency and longer-lasting equipment, the selection of the right secondary coupling device becomes essential. This article will explore ten expert-recommended options for secondary coupling devices that are renowned for their durability. By the end of this guide, you’ll have a comprehensive understanding of the best options available to enhance the longevity and effectiveness of your systems.
Flexible Disc Couplings: A Top Secondary Coupling Device for Misalignment
Flexible disc couplings are widely recognized as a top secondary coupling device for handling misalignment and absorbing shock loads. These couplings consist of a series of metal discs that are stacked together, allowing for flexibility in the transmission of torque. They are ideal for applications where there is a need to accommodate angular, parallel, or axial misalignment. The high-quality materials used in these couplings ensure long-term durability and resistance to wear. Experts recommend flexible disc couplings for their exceptional performance in high-speed and high-torque applications.
Universal Joint Couplings: Versatile Secondary Coupling Devices
Universal joint couplings, also known as U-joints, are versatile secondary coupling devices used to transmit torque between shafts that are not in line with each other. They are essential in applications where shafts need to operate at different angles. The design of universal joints allows for smooth and efficient power transmission, even under challenging conditions. These couplings are particularly praised for their robustness and ability to handle significant angular misalignment, making them a popular choice for various industrial applications.
Gear Couplings: Robust Secondary Coupling Devices for High Torque
Gear couplings are robust secondary coupling devices designed to transmit torque and accommodate angular and parallel misalignment between shafts. They consist of two hubs with internal gears that mesh together, providing a high level of torque transmission and flexibility. Gear couplings are known for their durability and ability to handle high torque loads and severe operating conditions. They are commonly used in applications such as pumps, compressors, and heavy machinery where reliable performance is crucial.
Elastomeric Couplings: Durable Secondary Coupling Devices for Noise Reduction
Elastomeric couplings use a flexible elastomeric element to transmit torque between shafts while absorbing shock and vibration. These durable secondary coupling devices are known for their ability to reduce noise and provide smooth operation, making them suitable for applications where noise reduction is a priority. The elastomeric element also provides a cushioning effect, which helps to protect equipment from potential damage caused by sudden shocks or misalignments. Experts recommend elastomeric couplings for their ease of maintenance and cost-effectiveness.
Magnetic Couplings
Magnetic couplings use magnetic fields to transmit torque between two shafts without physical contact. This contactless operation eliminates wear and tear on the coupling, resulting in a longer service life and reduced maintenance requirements. Magnetic couplings are particularly useful in applications where a hermetically sealed environment is necessary, such as in food processing and pharmaceutical industries. Their ability to operate in harsh environments and maintain precise control makes them a valuable option for various applications.
Chain Couplings
Chain couplings consist of two sprockets connected by a roller chain. They are known for their robustness and ability to handle heavy loads and high torque applications. Chain couplings are particularly effective in environments where there is a need for high torque transmission and resistance to shock loads. They are often used in applications such as conveyors, crushers, and mixers. Experts appreciate chain couplings for their durability and ease of maintenance, making them a reliable choice for demanding industrial settings.
Pin and Bush Couplings
Pin and bush couplings are designed to transmit torque while accommodating angular and parallel misalignment. These couplings use a series of pins and bushes to connect two shafts, providing a flexible and durable solution for power transmission. Pin and bush couplings are known for their high torque capacity and ability to handle significant misalignment. They are commonly used in applications where reliable performance and minimal maintenance are essential.
Rigid Couplings
Rigid couplings are designed to connect two shafts that are perfectly aligned, providing a solid and permanent connection. These couplings are used in applications where there is no need for misalignment compensation and where maximum torque transmission is required. Rigid couplings are known for their simplicity and durability, making them a cost-effective choice for applications where precise alignment is achievable. They are commonly used in machinery, pumps, and other equipment where a rigid connection is advantageous.
Bellows Couplings
Bellows couplings use a flexible bellows element to accommodate misalignment and absorb shock loads. The bellows element is typically made from stainless steel or other high-strength materials, providing excellent durability and resistance to wear. Bellows couplings are known for their ability to handle high speeds and maintain precise positioning, making them suitable for applications in robotics, automation, and precision machinery. Experts recommend bellows couplings for their flexibility and high-performance capabilities.
Oldham Couplings
Oldham couplings are designed to transmit torque between shafts that are misaligned in both angular and parallel directions. These couplings use a combination of three components – two hubs and a central disc – to provide a flexible and reliable connection. Oldham couplings are known for their ability to handle moderate misalignment and provide smooth operation in various applications. They are commonly used in stepper motors, servo motors, and other precision applications where alignment flexibility is important.
Conclusion
Selecting the right secondary coupling device is crucial for ensuring the durability and reliability of your machinery and equipment. The ten options discussed in this article – flexible disc couplings, universal joint couplings, gear couplings, elastomeric couplings, magnetic couplings, chain couplings, pin and bush couplings, rigid couplings, bellows couplings, and Oldham couplings – each offer unique advantages and are recommended by experts for their durability and performance. By considering the specific requirements of your application and the characteristics of each coupling type, you can make an informed decision that enhances the longevity and efficiency of your systems.
FAQs
1. What is the main advantage of flexible disc couplings?
Flexible disc couplings are highly effective at accommodating misalignment and absorbing shock loads, making them ideal for high-speed and high-torque applications.
2. How do magnetic couplings improve system performance?
Magnetic couplings transmit torque without physical contact, reducing wear and tear, and are particularly useful in environments requiring a sealed system, such as in the food processing industry.
3. Can a Secondary Coupling Device reduce maintenance costs?
Yes, a well-chosen Secondary Coupling Device can minimise wear and tear, reduce downtime, and extend the lifespan of primary components, leading to lower maintenance costs.
4. Are there different types of Secondary Coupling Devices for various industries?
There are various types of Secondary Coupling Devices, such as gear couplings, flexible disc couplings, and elastomeric couplings, each suited to different industrial needs.
5. How does a Secondary Coupling Device improve system performance?
A Secondary Coupling Device improves system performance by ensuring better alignment, reducing vibrations, and allowing for smoother power transmission between components.
Also read: Pinecones Caravan and Camping: 10 Must-Have Gear Items for Your Next Trip