Hard Manufacturing: Definition, Processes, and Industry Applications
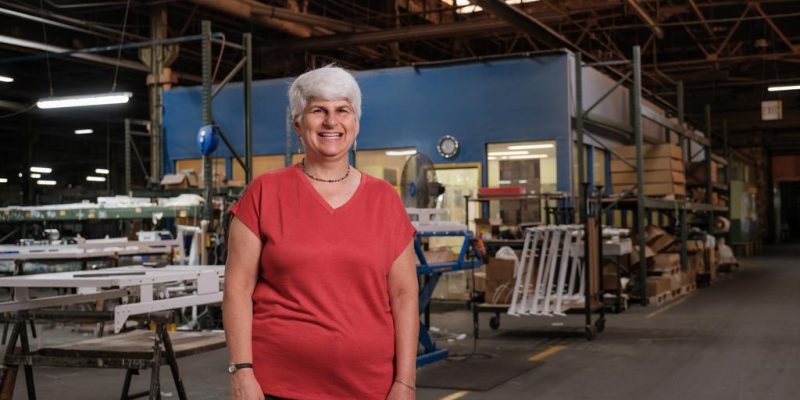
Hard manufacturing refers to the production of durable, high-strength products using materials like metals, ceramics, composites, and hardened plastics. Unlike soft manufacturing, which focuses on flexible materials like textiles or paper, hard manufacturing involves precision machining, heavy-duty processing, and specialized engineering techniques.
- This article will cover:
What is hard manufacturing?
Key processes in hard manufacturing
Industries that rely on hard manufacturing
Advantages and challenges of hard manufacturing
Future trends in hard manufacturing
Let’s dive into the world of hard manufacturing and explore how it shapes modern industries.
What is Hard Manufacturing?
- Hard manufacturing is a manufacturing process that focuses on producing strong, durable, and rigid products from materials such as:
Metals (steel, aluminum, titanium)
Ceramics (silicon carbide, zirconia)
Composites (carbon fiber, Kevlar)
Hardened plastics (polycarbonate, PEEK)
Example: The production of automobile engines, aircraft components, medical implants, and industrial machinery falls under hard manufacturing.
- Key Characteristics of Hard Manufacturing:
Requires high-precision machinery and advanced technology.
Uses heat treatment, forging, casting, and CNC machining.
Produces long-lasting, high-performance products.
Key Processes in Hard Manufacturing
CNC Machining (Computer Numerical Control)
- Uses automated cutting tools to shape metal and hard materials.
Ensures high precision in aerospace, automotive, and medical industries.
Example: CNC machines are used to cut titanium parts for aircraft engines.
Metal Casting & Forging
- Casting: Molten metal is poured into a mold to create parts.
Forging: Metal is compressed and shaped under heat and pressure.
Example: Automobile manufacturers use forging for engine crankshafts and gears.
Additive Manufacturing (3D Printing for Hard Materials)
- Creates complex designs using metal and composite powders.
Reduces material waste compared to traditional manufacturing.
Example: Medical implants (like titanium hip replacements) are produced via 3D printing.
Injection Molding for Hardened Plastics
- Used to manufacture strong plastic components for industries like electronics and automotive.
Example: Polycarbonate panels for bulletproof glass and safety helmets.
Heat Treatment & Surface Hardening
- Improves the strength, durability, and wear resistance of metal components.
Example: Carbide coatings on drill bits increase their lifespan and performance.
Industries That Rely on Hard Manufacturing
Hard manufacturing plays a crucial role in several industries, including:
- Aerospace & Defense
- Aircraft parts (turbines, fuselage components)
Military equipment (armored vehicles, missile casings)
Why it’s important: Extreme durability and precision are required for safety and performance.
Automotive Manufacturing
- Engine parts (pistons, crankshafts)
Chassis and body panels
Why it’s important: Cars require high-strength metals and composites for safety and efficiency.
Medical Device Manufacturing
- Titanium implants (hip and knee replacements)
Surgical tools and dental implants
Why it’s important: Medical products must be biocompatible, strong, and long-lasting.
Electronics & Semiconductor Industry
- Hard plastic casings for smartphones and laptops
Microchip and circuit board manufacturing
Why it’s important: Precision and durability are essential for high-performance electronics.
Heavy Machinery & Industrial Equipment
- Mining and construction tools
Manufacturing robots and factory automation
Why it’s important: Equipment must withstand harsh environments and heavy use.
Advantages & Challenges of Hard Manufacturing
- Advantages
- High Durability: Products last longer and perform better under stress.
Precision & Consistency: Advanced machining ensures accurate and repeatable results.
Strong Material Properties: Metals, composites, and ceramics resist heat, corrosion, and wear. - Challenges
- High Production Costs: Requires expensive machines, tools, and raw materials.
Longer Production Time: Hard materials are more difficult to machine and process.
Environmental Impact: Metal and plastic manufacturing can generate waste and emissions.
Future Trends in Hard Manufacturing
AI & Automation in Manufacturing
- Smart robotic systems improve precision and reduce human error.
AI-driven predictive maintenance prevents machine breakdowns.
Example: Self-adjusting CNC machines optimize cutting speed and efficiency.
Sustainable Manufacturing
- Increased use of recycled metals and eco-friendly composites.
Development of low-waste production methods.
Example: Tesla’s gigafactories use sustainable methods for battery and car production.
Advancements in Additive Manufacturing (Metal 3D Printing)
- More industries are adopting 3D printing for metal parts, reducing material waste.
New lightweight and ultra-strong alloys improve efficiency.
Example: GE Aviation uses 3D-printed turbine blades in jet engines.
Nanotechnology & Advanced Coatings
- Nanocoatings enhance the durability of machine parts.
Self-healing materials reduce wear and tear over time.
Example: Scratch-resistant coatings on smartphones improve longevity.
Conclusion
Hard manufacturing is the backbone of modern industries, from aerospace to medical devices. As technology advances, the industry is shifting towards automation, sustainability, and precision engineering.
Key Takeaways:
- Hard manufacturing produces strong, durable, and high-performance products.
Key processes include CNC machining, metal forging, and 3D printing.
Industries like automotive, aerospace, and medical devices rely on hard manufacturing.
Future trends include AI automation, sustainable materials, and nanotechnology.
Do you work in hard manufacturing? Share your thoughts and experiences in the comments!
FAQs
1. What is hard manufacturing?
Hard manufacturing is the production of strong, durable products using metals, ceramics, composites, and hardened plastics.
2. How is hard manufacturing different from soft manufacturing?
Hard manufacturing deals with rigid materials like metals, while soft manufacturing focuses on flexible materials like textiles and paper.
3. What industries use hard manufacturing?
Aerospace, automotive, medical devices, electronics, and heavy machinery industries all rely on hard manufacturing.
4. What are the biggest challenges in hard manufacturing?
High costs, long production times, and environmental impact are major challenges.
5. What’s the future of hard manufacturing?
Automation, sustainable materials, and advanced 3D printing are shaping the future of hard manufacturing.
Also read: Hiring Your Parents for Your Business: Benefits, Legal Considerations, and Tax Advantages